CFD Analysis of Stirred Tank Reactor (CSTR)
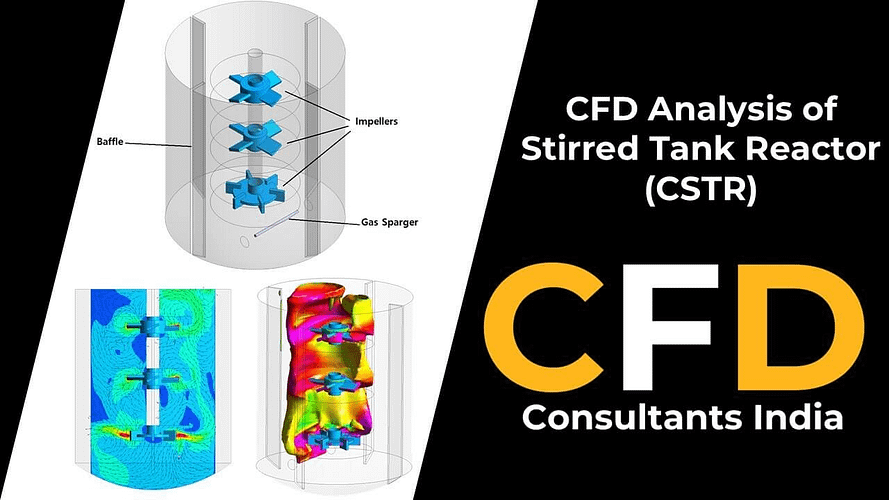
Introduction to Stirred Tank Reactor (CSTR)
Continuous Stirred-Tank Reactors (CSTRs) play a crucial role in industries such as chemical processing, pharmaceuticals, and bioreactors. Ensuring optimal mixing, reaction rates, and mass transfer efficiency within a CSTR is essential for its effective operation. In this case study, we explore a recent Computational Fluid Dynamics (CFD) analysis conducted on a multiphase CSTR designed for bioreactor applications. The reactor features baffles on the tank wall, three impellers mounted on a single agitator shaft, and a gas sparger positioned at the bottom. The analysis aimed to optimize the reactor’s performance and address challenges associated with multiphase flow in bioreactors.
The project involved a detailed CFD simulation of a CSTR used in bioreactor applications. The reactor’s design included:
Baffles: Mounted on the tank wall, these baffles were included to disrupt vortex formation and improve mixing efficiency.
Three Impellers: Positioned on a single agitator shaft, these impellers were critical in enhancing the mixing of reactants and ensuring uniform distribution within the reactor.
Gas Sparger: Located at the bottom of the reactor, the gas sparger introduced gases into the liquid phase, essential for processes requiring efficient gas-liquid mass transfer, such as those in bioreactors.
CFD Methodology
The CFD analysis employed advanced multiphase modeling techniques to accurately simulate the complex interactions between the gas and liquid phases within the reactor. The key steps in the methodology included:
Geometry and Mesh Generation: The reactor’s geometry was modeled, including the baffles, impellers, and gas sparger. A high-quality mesh was created to capture the intricate flow patterns and interactions within the reactor, particularly around the baffles and impellers.
Multiphase Flow Modeling: The Volume of Fluid (VOF) method was used to track the interface between the gas and liquid phases. The Eulerian approach was applied to model the dispersed gas phase, capturing the behavior of bubbles as they interacted with the liquid.
Turbulence Modeling: Due to the complex flow patterns caused by the impellers and the presence of baffles, a suitable turbulence model, such as the k-epsilon or Reynolds Stress Model (RSM), was used to accurately predict the turbulent mixing within the reactor.
Simulation Setup and Boundary Conditions: The reactor was initialized with realistic boundary conditions, including gas flow rates, liquid properties, and operating conditions relevant to bioreactor applications. The impeller rotation was modeled using either the Multiple Reference Frame (MRF) or Sliding Mesh approach.
Post-Processing and Analysis: The results of the simulation were analyzed to evaluate key performance indicators such as mixing efficiency, gas hold-up, and the effectiveness of the baffles. Flow visualizations, including velocity vectors, phase distribution, and turbulence intensity, provided insights into the reactor’s behavior.
Results and Insights
The CFD analysis revealed several key insights into the performance of the CSTR:
Enhanced Mixing: The combination of baffles and impellers significantly improved mixing within the reactor. The baffles disrupted vortex formation, leading to a more uniform distribution of reactants and preventing the formation of dead zones.
Improved Gas-Liquid Mass Transfer: The gas sparger, when combined with the optimized impeller design, facilitated effective gas-liquid mass transfer, a critical factor in bioreactor applications. The VOF model successfully captured the gas hold-up and bubble distribution within the reactor.
Turbulence Control: The presence of baffles enhanced the turbulence in the reactor, ensuring that the flow remained well-mixed and that mass transfer processes were efficient. This was particularly important in preventing the stratification of phases.
Conclusion
This case study demonstrates the value of advanced CFD analysis in optimizing the design and performance of a CSTR, particularly for bioreactor applications. By employing sophisticated multiphase flow modeling and turbulence analysis, the study provided actionable insights to enhance reactor efficiency. The successful implementation of baffles, impeller configuration, and gas sparger design underscores the importance of CFD in addressing complex engineering challenges in bioreactors.
This case study highlights how CFD can be leveraged to improve reactor design and operation, leading to more efficient and reliable bioprocessing solutions. For more information on how our CFD expertise can benefit your bioreactor applications, For more information and professional CFD consulting services, visit mail us on info(at)cfdconsultantsindia.com
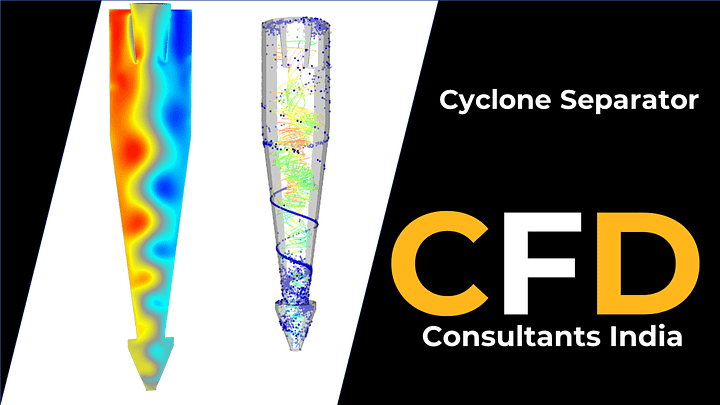
Read out how CFD analysis improves the separation efficiency of cyclone separators. Learn how the study identifies flow patterns, particle trajectories, and proposes design modifications for enhanced performance.
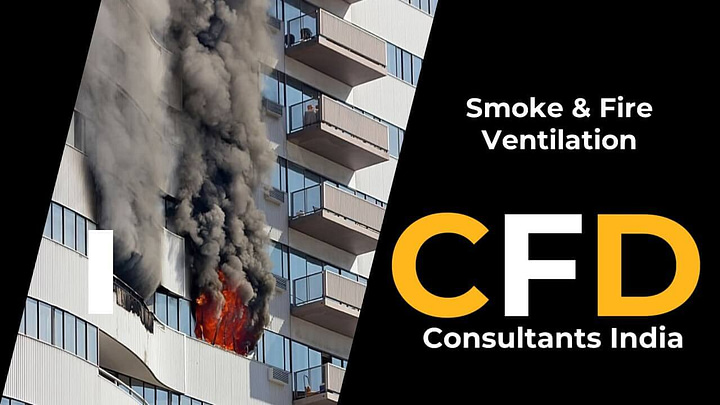
Ensure the safety of occupants, compliance regulations with CFD analysis for fire and smoke ventilation systems in the event of fire & smoke.
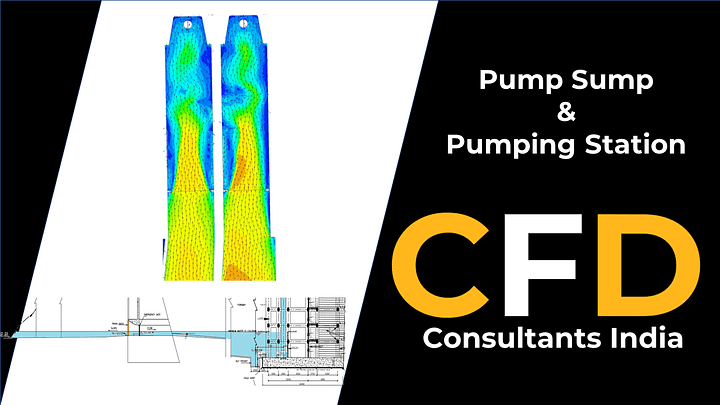
Enhance the performance of your pumping system with CFD analysis of pump sump and pumping station. Discover how to improve flow uniformity, prevent vortex formation, and enhance pump efficiency for optimal operation.
Let's stay in touch!
To get recent updates, stay connect us on our LinkedIn page! Don’t hesitate to reach out to us for any questions, concerns or future collaborations
Contact Us
We are here to help! With just a quick input details we will be able to respond to your inquiry.
E-Mail: info(at)cfdconsultantsindia.com
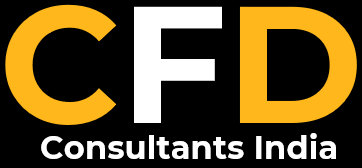
CFD Consultants India a leading provider of CFD simulation consultation and services. We use finite volume computation technique to predict the flow behavior using various commercial CFD software’s. At CFD Consultants India, we understand the importance of accurate and reliable CFD simulations in the design and development process. With years of experience and expertise in the field, we offer customized solutions to meet your specific requirements and help you achieve your goals.
Whether you are looking to optimize your product design, improve performance, reduce costs, or enhance safety, CFD Consultants India can help. Contact us today to learn more about our services and how we can help you achieve your goals.
© Copyright CFD Consultants India 2023 | All rights reserved.