CFD Analysis of Mist Eliminator
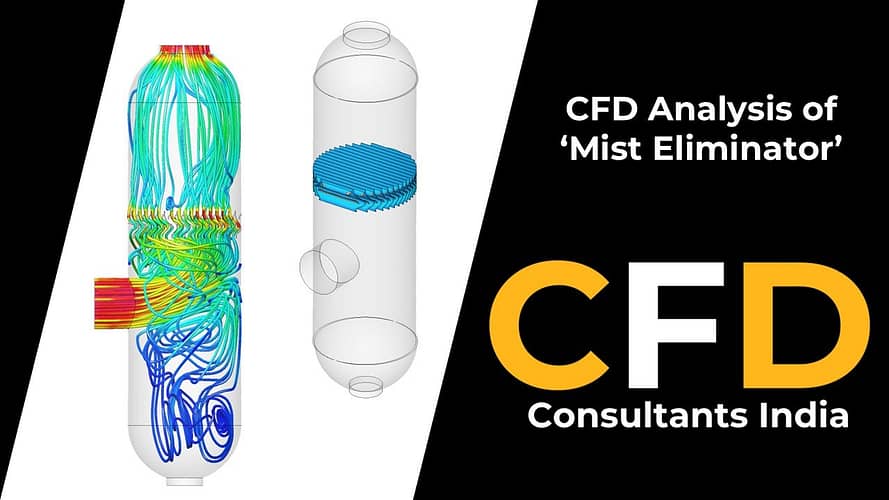
Introduction to Mist Eliminator
Mist eliminators are essential components in industrial processes where gas streams contain liquid droplets, such as in chemical plants, refineries, and gas processing units. Their primary function is to remove these droplets from the gas flow, preventing them from being carried downstream. This is crucial for protecting equipment, ensuring product quality, and maintaining environmental compliance.
How Mist Eliminators Work: Mist eliminators operate on the principle of impingement, where gas flows through a mesh or vane structure designed to create a tortuous path. As the gas stream navigates this path, liquid droplets are forced to collide with the surfaces of the eliminator. Upon impact, these droplets coalesce, grow larger, and eventually drain away under gravity, leaving a cleaner gas stream to exit the system.
Types of Mist Eliminators:
- Wire Mesh Mist Eliminators: These are made from layers of woven or knitted wire mesh and are effective at removing fine droplets. They are commonly used in low to moderate gas velocity applications.
- Vane Type Mist Eliminators: These consist of a series of parallel plates (vanes) that cause the gas stream to change direction multiple times, enhancing droplet separation. They are suitable for higher velocity applications.
- Fiber Bed Mist Eliminators: Comprising densely packed fibers, these eliminators are highly efficient at capturing submicron droplets. They are used in applications requiring extremely high separation efficiency.
This case study presents a Computational Fluid Dynamics (CFD) analysis conducted to evaluate and optimize the performance of a vane type mist eliminator installed in a gas scrubber of a petrochemical plant. The objective was to diagnose the causes of liquid carryover and implement design modifications to enhance the mist eliminator’s efficiency.
Problem Statement
The petrochemical plant had been experiencing issues with liquid carryover, leading to operational inefficiencies and increased maintenance costs. The mist eliminator installed in the gas scrubber was suspected to be underperforming, resulting in inadequate separation of liquid droplets from the gas stream. The primary goal of the CFD analysis was to assess the current performance of the mist eliminator and provide comparative separation efficiency and pressure drop results on available vane designs in terms of spacing and shape modifications to enhance its efficiency.
CFD Methodology
Based on the inputs and design specifications provided by the client, a detailed 3D model of the mist eliminator and its surrounding environment was created in the CFD software. The model included all relevant components, such as the mist eliminator vanes, support structures, and the geometry of the gas scrubber.
To simulate the real-world conditions, a CFD wind tunnel was created, incorporating the nearby equipment and structural elements. All potential obstructions, including the eliminator’s mesh structure, were modeled with high accuracy.
Appropriate boundary conditions were applied, considering the inlet gas velocity, droplet size distribution, and the pressure at the outlet. The wind and ambient conditions were set according to the project requirements and site location, ensuring the simulation accurately represented the operational environment.
After completing the model, a steady-state CFD simulation was performed to study the gas velocity distribution, droplet capture efficiency, and the percentage of liquid carryover. The results were analyzed to identify areas of high velocity, recirculation zones, and regions where the mist eliminator was underperforming.
Conclusion
The CFD simulation revealed critical insights into the performance of the mist eliminator. It was observed that the gas flow was unevenly distributed across the mist eliminator, leading to insufficient droplet capture in certain areas. This uneven distribution resulted in a liquid carryover of approximately 10-15%, which was higher than the acceptable limit.
The simulation also identified recirculation zones where captured droplets were being re-entrained into the gas stream, further reducing the efficiency of the mist eliminator.
Based on these findings, design modifications were proposed, including adjustments to the vane angles and mesh density to improve gas flow distribution and increase droplet capture efficiency. The modifications were re-simulated, resulting in a significant improvement, with the liquid carryover reduced to less than 5% and the overall efficiency of the mist eliminator increased to over 95%.
The study successfully provided the client with actionable insights and recommendations, leading to enhanced performance of the mist eliminator and reduced operational issues in the petrochemical plant.
This case study highlights how CFD can be leveraged to improve design and operation, leading to more efficient and reliable solutions. For more information on how our CFD expertise can benefit your mist eliminator, For more information and professional CFD consulting services, visit mail us on info(at)cfdconsultantsindia.com
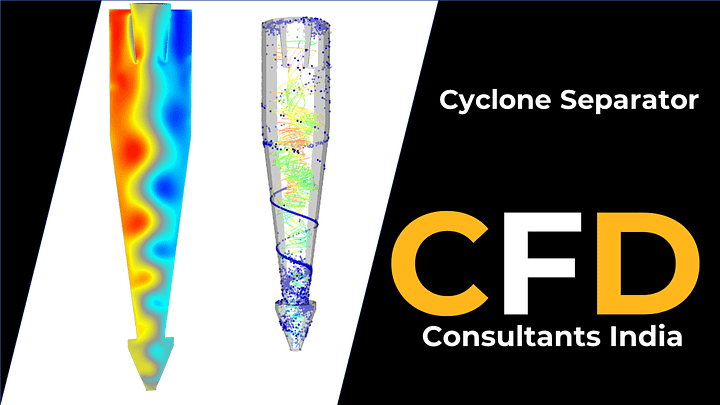
Read out how CFD analysis improves the separation efficiency of cyclone separators. Learn how the study identifies flow patterns, particle trajectories, and proposes design modifications for enhanced performance.
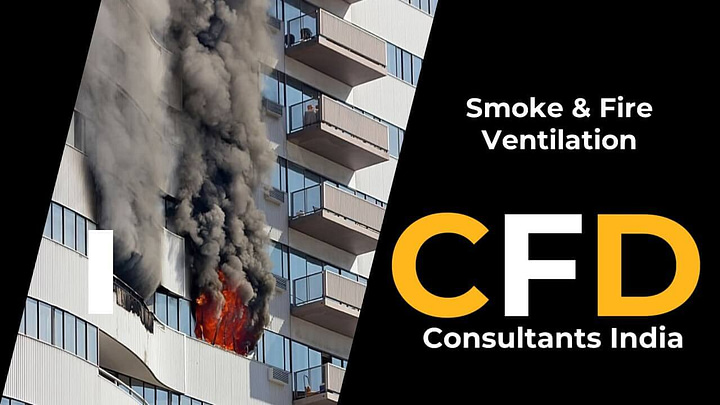
Ensure the safety of occupants, compliance regulations with CFD analysis for fire and smoke ventilation systems in the event of fire & smoke.
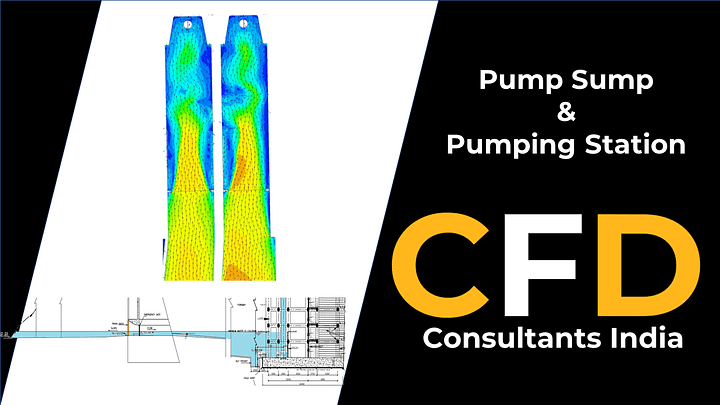
Enhance the performance of your pumping system with CFD analysis of pump sump and pumping station. Discover how to improve flow uniformity, prevent vortex formation, and enhance pump efficiency for optimal operation.
Let's stay in touch!
To get recent updates, stay connect us on our LinkedIn page! Don’t hesitate to reach out to us for any questions, concerns or future collaborations
Contact Us
We are here to help! With just a quick input details we will be able to respond to your inquiry.
E-Mail: info(at)cfdconsultantsindia.com
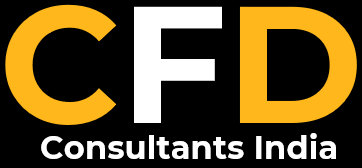
CFD Consultants India a leading provider of CFD simulation consultation and services. We use finite volume computation technique to predict the flow behavior using various commercial CFD software’s. At CFD Consultants India, we understand the importance of accurate and reliable CFD simulations in the design and development process. With years of experience and expertise in the field, we offer customized solutions to meet your specific requirements and help you achieve your goals.
Whether you are looking to optimize your product design, improve performance, reduce costs, or enhance safety, CFD Consultants India can help. Contact us today to learn more about our services and how we can help you achieve your goals.
© Copyright CFD Consultants India 2023 | All rights reserved.