CFD Analysis of Electronic Cooling System
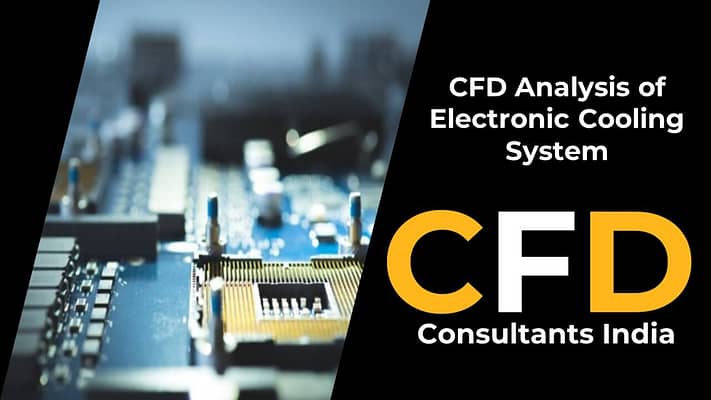
Introduction
In this case study, we conducted a CFD analysis of an electronic cooling system to improve its thermal management capabilities and ensure optimal performance of electronic components. By utilizing Computational Fluid Dynamics (CFD), we aimed to understand the heat transfer mechanisms, airflow patterns, and temperature distribution within the cooling system. The analysis provided valuable insights for optimizing the design and operation of the electronic cooling system.
Methodology
1. System Geometry and Meshing
A detailed three-dimensional model of the electronic cooling system was developed, considering the heat-generating electronic components such as CPU, GPU and other heating chips along with heat sinks, fans, and airflow channels. The geometry was carefully constructed to capture the intricacies of the system. An appropriate mesh was generated with fine meshing near heat generating elements to accurately resolve the flow field and temperature gradients within the system.
2. Heat Transfer and Fluid Flow Simulation
The CFD analysis focused on simulating the heat transfer and fluid flow phenomena within the electronic cooling system. The heat generated by electronic components was modeled as a heat source, and the convective heat transfer between the components and the surrounding air was accounted for. The airflow patterns and velocity distribution were analyzed to ensure effective cooling.
3. Fan Performance Modeling
To accurately simulate the cooling system, the performance of the fans was modeled based on fan curves or experimental data. The fan characteristics, such as flow rate and pressure drop, were incorporated into the simulation. This allowed for a realistic representation of the airflow generated by the fans and its impact on cooling efficiency.
4. Temperature Distribution and Cooling Effectiveness
The CFD analysis provided insights into the temperature distribution within the electronic cooling system. The thermal gradients and hotspots were identified, enabling the optimization of heat sink placement, airflow channels, and fan positioning. The cooling effectiveness of the system was evaluated by analyzing the temperature reduction achieved by the cooling components.
Results and Conclusion
The CFD analysis of the electronic cooling system yielded the following outcomes:
1. Optimal Heat Sink Design: By analyzing the temperature distribution and airflow patterns, areas of inadequate heat transfer or hotspots were identified. This information guided the design modifications to improve heat sink performance and enhance cooling effectiveness.
2. Airflow Optimization: The simulation results allowed for the optimization of airflow channels and fan positioning to ensure efficient cooling. The analysis helped identify areas of recirculation or stagnant airflow, enabling design improvements to enhance cooling efficiency.
3. Cooling System Performance Evaluation: The CFD analysis facilitated the evaluation of different operating conditions, such as fan speed and flow rate, to assess their impact on cooling performance. This information guided the selection of optimal operating parameters for enhanced cooling efficiency.
In conclusion, the CFD analysis of the electronic cooling system provided valuable insights into the heat transfer and airflow dynamics within the system. By optimizing the design and operating parameters based on the simulation results, the thermal management capabilities were improved, ensuring optimal performance and reliability of the electronic components.
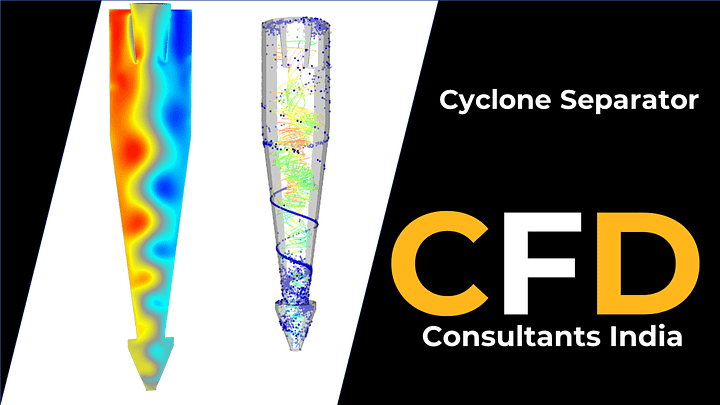
Read out how CFD analysis improves the separation efficiency of cyclone separators. Learn how the study identifies flow patterns, particle trajectories, and proposes design modifications for enhanced performance.
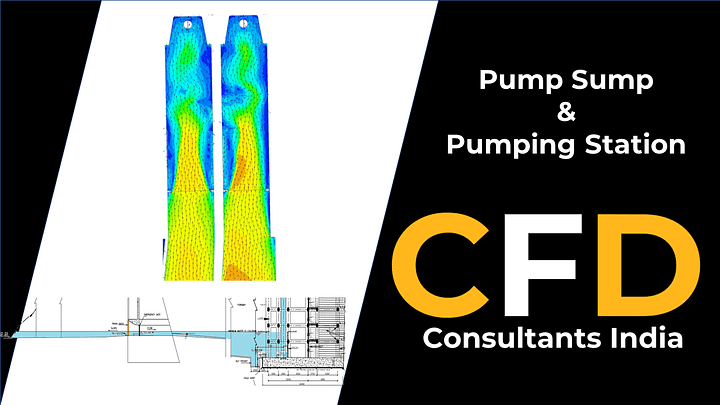
Enhance the performance of your pumping system with CFD analysis of pump sump and pumping station. Discover how to improve flow uniformity, prevent vortex formation, and enhance pump efficiency for optimal operation.
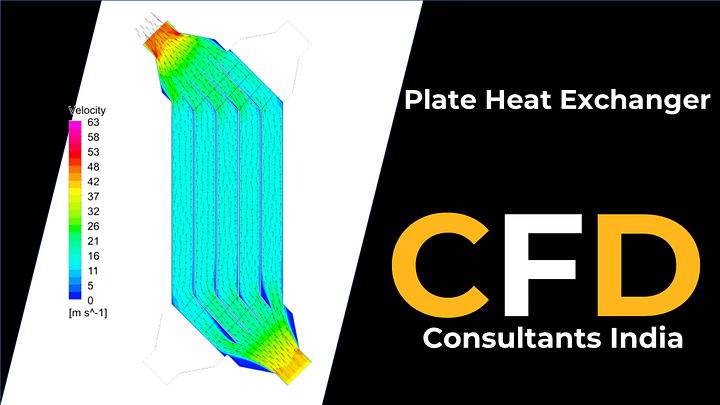
Enhance the performance and efficiency of your plate heat exchanger through CFD analysis. Discover how design modifications can improve heat transfer efficiency, reduce energy costs, and optimize operation.
Let's stay in touch!
To get recent updates, stay connect us on our LinkedIn page! Don’t hesitate to reach out to us for any questions, concerns or future collaborations
Contact Us
We are here to help! With just a quick input details we will be able to respond to your inquiry.
E-Mail: info(at)cfdconsultantsindia.com
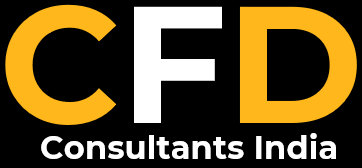
CFD Consultants India a leading provider of CFD simulation consultation and services. We use finite volume computation technique to predict the flow behavior using various commercial CFD software’s. At CFD Consultants India, we understand the importance of accurate and reliable CFD simulations in the design and development process. With years of experience and expertise in the field, we offer customized solutions to meet your specific requirements and help you achieve your goals.
Whether you are looking to optimize your product design, improve performance, reduce costs, or enhance safety, CFD Consultants India can help. Contact us today to learn more about our services and how we can help you achieve your goals.
© Copyright CFD Consultants India 2023 | All rights reserved.